Porosity in Welding: Identifying Common Issues and Implementing Ideal Practices for Avoidance
Porosity in welding is a prevalent concern that frequently goes unnoticed till it causes substantial troubles with the integrity of welds. This common issue can compromise the stamina and toughness of bonded structures, positioning security dangers and resulting in expensive rework. By comprehending the source of porosity and executing effective prevention approaches, welders can dramatically enhance the top quality and dependability of their welds. In this discussion, we will certainly check out the vital elements contributing to porosity formation, analyze its detrimental effects on weld efficiency, and discuss the very best methods that can be adopted to minimize porosity event in welding processes.
Usual Causes of Porosity
One more frequent wrongdoer behind porosity is the existence of pollutants on the surface area of the base steel, such as oil, grease, or rust. When these contaminants are not efficiently gotten rid of prior to welding, they can evaporate and become trapped in the weld, creating flaws. In addition, using filthy or damp filler materials can introduce impurities right into the weld, adding to porosity concerns. To reduce these usual causes of porosity, thorough cleansing of base metals, proper shielding gas choice, and adherence to ideal welding specifications are crucial techniques in accomplishing high-quality, porosity-free welds.
Effect of Porosity on Weld Quality

The existence of porosity in welding can considerably compromise the structural honesty and mechanical buildings of bonded joints. Porosity produces spaces within the weld metal, deteriorating its overall stamina and load-bearing capability.
Among the main consequences of porosity is a decrease in the weld's ductility and toughness. Welds with high porosity degrees have a tendency to exhibit reduced impact stamina and lowered ability to deform plastically before fracturing. This can be specifically concerning in applications where the welded components undergo check my site dynamic or cyclic loading conditions. Porosity can hamper the weld's capability to successfully transmit pressures, leading to early weld failure and prospective security hazards in critical structures. What is Porosity.
Best Practices for Porosity Prevention
To enhance the architectural honesty and top quality of bonded joints, what certain measures can Go Here be carried out to minimize the incident of porosity during the welding procedure? Using the proper welding strategy for the certain product being bonded, such as readjusting the welding angle and weapon setting, can further protect against porosity. Normal examination of welds and immediate remediation of any type of concerns recognized throughout the welding procedure are essential methods to stop porosity and generate high-grade welds.
Relevance of Proper Welding Techniques
Carrying out appropriate welding methods is extremely important in making sure the structural stability and top quality of bonded joints, developing upon the foundation of reliable porosity avoidance actions. Extreme warm can lead to boosted porosity due to the entrapment of gases in the weld pool. Additionally, using the appropriate welding specifications, such as voltage, present, and take a trip speed, is important for achieving sound welds with very little porosity.
In addition, the choice of welding process, whether it be MIG, TIG, or stick welding, need to line up with the specific requirements of the task to ensure optimal results. Proper cleaning and preparation of the base steel, as well as selecting the best filler material, are also essential parts of skillful welding strategies. By sticking to these ideal techniques, welders can lessen the danger of porosity development and produce premium, structurally audio welds.
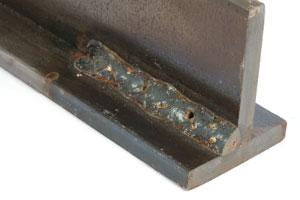
Evaluating and Quality Assurance Procedures
Quality control measures play an important duty in verifying the stability and integrity of bonded joints. Examining procedures are important to identify and protect against porosity in welding, making certain the strength and longevity discover here of the last item. Non-destructive screening methods such as ultrasonic testing, radiographic testing, and aesthetic assessment are typically employed to identify potential defects like porosity. These techniques permit the analysis of weld quality without endangering the honesty of the joint. What is Porosity.
Performing pre-weld and post-weld evaluations is also critical in keeping quality assurance requirements. Pre-weld assessments include validating the products, equipment settings, and tidiness of the workspace to stop contamination. Post-weld evaluations, on the various other hand, examine the final weld for any defects, including porosity, and confirm that it satisfies defined standards. Carrying out a comprehensive quality assurance strategy that consists of complete screening treatments and examinations is paramount to lowering porosity problems and guaranteeing the total high quality of welded joints.
Verdict
In final thought, porosity in welding can be a common problem that influences the top quality of welds. By identifying the usual reasons for porosity and carrying out finest practices for prevention, such as proper welding techniques and screening steps, welders can guarantee high top quality and trusted welds. It is essential to focus on avoidance methods to reduce the event of porosity and maintain the honesty of bonded frameworks.